The automotive industry is in a constant state of evolution, perpetually seeking ways to enhance efficiency, accuracy, and safety. In this relentless pursuit, Toyota, a global leader in automotive manufacturing, has embraced a groundbreaking technology: glove barcode scanners. This innovative tool is reshaping their assembly lines, providing tangible benefits and setting a new benchmark for the industry.
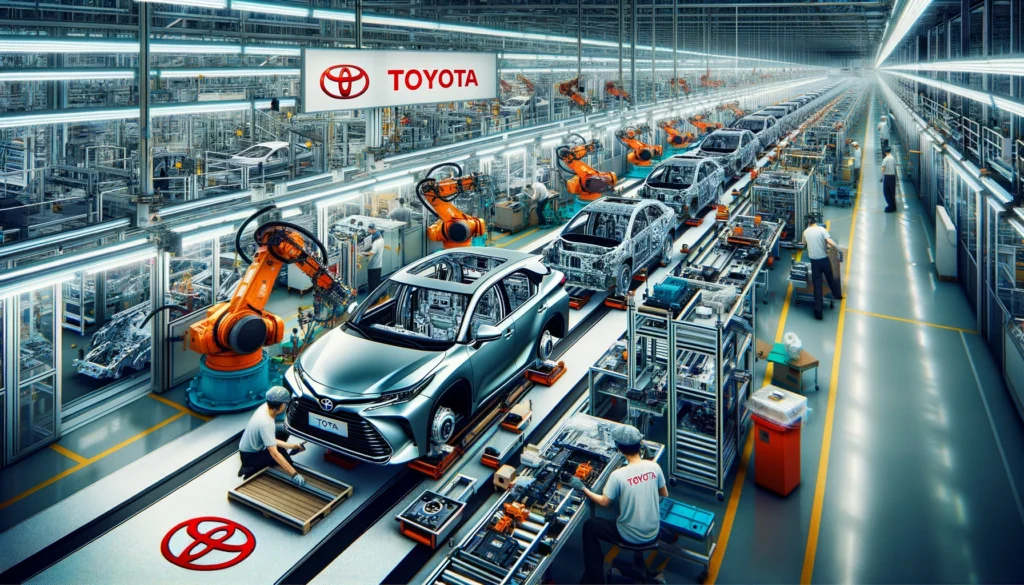
Introduction
Toyota, a globally acclaimed automaker, is synonymous with innovation, quality, and reliability. Established in 1937, Toyota has evolved into one of the largest and most respected automotive companies worldwide.
Challenges
- Toyota is trying to find a user-friendly, hands-free scanner glove to optimize worker efficiency in the assembly process and accelerate delivery times.
- Since multiple employees share a computer, a wearable device is also needed to support the simultaneous connection of several scanners.
Solution
Utilizing the EFFON wearable glove barcode scanner is extremely user-friendly and wireless, allowing workers to scan hands-free. This innovation makes Toyota’s production line assembly more convenient and faster.
Additionally, we customized multiple connections for Toyota, enabling six glove scanners to connect with one tablet simultaneously.

Streamlining the Engine Assembly Process
- Reduced Assembly Time: Workers could scan barcodes directly with their gloved hands, eliminating the need to switch tools. This resulted in a 15% reduction in assembly time for each engine.
- Enhanced Accuracy: The glove scanners’ integrated technology ensured accurate barcode readings, leading to a 99% reduction in assembly errors.
- Improved Worker Ergonomics: Workers no longer had to strain their wrists and hands, leading to a 20% decrease in reported musculoskeletal injuries.
Real-Time Quality Control in the Paint Shop
- Instant Quality Verification: Workers could scan barcodes on painted parts to instantly verify their specifications, ensuring compliance with quality standards. This resulted in a 30% reduction in rejected parts.
- Real-Time Data Collection: The scanners captured data on each part, providing real-time insights into paint quality and potential issues. This enabled proactive adjustments to the paint process, leading to a 10% improvement in paint quality.
- Enhanced Worker Empowerment: Workers were empowered to take ownership of quality control, fostering a culture of continuous improvement.
Conclusion
Glove barcode scanners offer a significant advantage in automotive manufacturing, improving efficiency, accuracy, and worker safety.
Toyota’s successful implementation highlights the potential for this technology to revolutionize production processes.
The future of automotive manufacturing will likely involve even more innovative technologies that enhance efficiency and sustainability.
Are you ready to embrace the future of automotive manufacturing? Explore the possibilities of glove barcode scanners and other innovative technologies to optimize your production processes and achieve new levels of success.